Can pressure sensors measure vacuum?
Yes, a pressure sensor can measure vacuum( -100KPa~0KPa). But only if it is specifically designed as a “vacuum pressure sensor” and calibrated to measure pressure below atmospheric pressure (negative gauge pressure). Standard pressure sensors can only measure pressure above atmospheric pressure, so they cannot directly measure vacuum.
To measure vacuum, you need a pressure sensor that measures “gauge pressure”. This pressure sensor is relative to atmospheric pressure. This means that negative readings indicate a vacuum. These sensors are specifically designed to measure pressure below atmospheric pressure and can accurately convert the vacuum level into an electrical signal.
What is a vacuum pressure Transducer?
A vacuum pressure transducer is a device that measures pressure below atmospheric pressure. It does this by detecting the difference between the pressure inside the system and the surrounding atmospheric pressure. This pressure difference is converted into an electrical signal that can be read and analyzed. It is measured in units such as Torr, inches of mercury (inHg), or Pascals (Pa).
These transducers are essential in a variety of applications, such as vacuum pumps, chambers, and systems.
Common vacuum pressure transducer types:
- Capacitive transducers:
They use the change in capacitance between a diaphragm and a fixed electrode to measure pressure. - Piezoelectric transducers:
When pressure is applied to a piezoelectric material, it generates an electrical charge proportional to the pressure. - Strain gauge transducers:
They use the change in resistance of a strain gauge connected to a diaphragm to measure pressure.
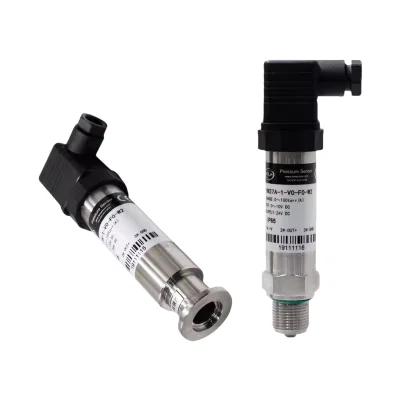
Working principle of vacuum pressure Transducers
The working principle of vacuum pressure transducer is to detect the deflection of the diaphragm caused by the pressure difference between the vacuum environment and the atmospheric pressure. The greater the pressure difference, the greater the diaphragm deflection, thus generating a stronger electrical signal.
Key points about vacuum pressure sensors:
- Diaphragm deflection:
The core component is a flexible diaphragm. When exposed to a vacuum, the diaphragm bends inward, which means the pressure is lower than the surrounding atmosphere.
- Sensing element:
This element is similar to a strain gauge or a capacitive plate. It is connected to the diaphragm and detects its movement, converting it into an electrical signal.
- Electrical signal output:
The sensor outputs an electrical signal that is proportional to the pressure difference. Thus, the vacuum level can be measured and analyzed.
Applications of vacuum pressure transducers
Vacuum pressure transducers are widely used in many fields. In industrial automation environments, the automotive industry, and brake systems, they are used to monitor and control vacuum environments to ensure process integrity and safety. Basically, anywhere low pressure needs to be accurately monitored and regulated.
Main applications of vacuum pressure transducers:
- Semiconductor Manufacturing: Maintaining precise vacuum conditions during chip manufacturing.
- Vacuum Packaging: Monitoring vacuum levels in sealed food packages to extend shelf life.
- Medical Devices: Regulating vacuum levels in suction devices and other medical instruments.
- Aerospace Applications: Monitoring pressure in spacecraft and vacuum chambers during testing.
- Automotive Industry: Vacuum-assisted gripping systems in assembly lines, windshield installation.
- Chemical Processing: Controlling vacuum levels during distillation and filtration.
- Research Laboratories: Creating and monitoring controlled vacuum environments for experiments.
- Environmental Monitoring: Measuring atmospheric pressure and air quality.
- Leak Detection: Identifying leaks in vacuum systems by monitoring pressure changes.
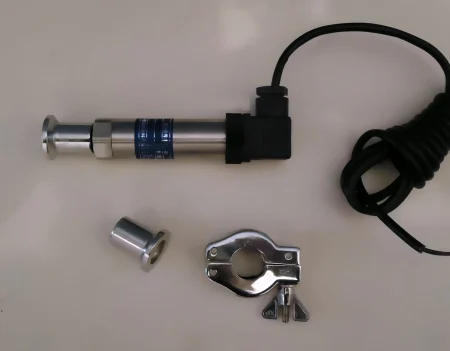
Pressure transducers vs. pressure sensors
Sensors and Transducers are actually the same thing. The main difference is the type of electrical signal they each send. A pressure sensor converts pressure into an electrical signal, usually a voltage. Whereas a pressure transducer takes that signal and further processes it to produce a standardized current output, such as 4-20 mA. This is more suitable for long-distance transmission in industrial applications.
Compared to sensors, transducers include additional circuitry for amplification and signal conditioning. Sensors send signals in volts (V) or millivolts (mV), while transducers send signals in milliamperes (mA).
Main differences:
Difference | Pressure sensor | Pressure Transducer |
Output | Pressure sensors usually output voltage | Pressure transducers output current (such as 4-20 mA) |
Signal processing | ressure sensors convert the raw electrical signal into digital form | Pressure transducers have additional circuitry for signal amplification,linearization and temperature compensation |
Applications | Pressure sensors are often used in applications that require a simple voltage output | Pressure transducers are the preferred choice for transmitting signals over long distances in industrial environments. |
Types of pressure
In industrial environments, the main types of pressure measured are: absolute pressure, gauge pressure, and differential pressure. These are usually measured using pressure sensors. Pressure sensors are an important part of monitoring and controlling pressure in industrial processes.
The main types of industrial pressure include the following:
- Absolute pressure:
Measures pressure relative to a complete vacuum and is considered the most accurate pressure measurement. Because it uses a complete vacuum as a reference point. It is often used in scientific applications and industries that require high-precision pressure measurements. Such as chemicals, pharmaceuticals, and food processing.
- Gauge pressure:
Measures pressure relative to the surrounding atmospheric pressure and is often used for everyday pressure measurements. This is the most common type of pressure measurement in industrial applications.
- Differential pressure:
Measures the difference in pressure between two points in a system. It measures the flow rate in a pipeline by comparing the pressure before and after the flow restriction. It is essential for monitoring flow and identifying pressure imbalances in industrial processes.
- Vacuum pressure:
Vacuum pressure is pressure below atmospheric pressure, also known as negative pressure. The working pressure is less than 0MPa. It is often used in vacuum packaging and laboratory environments.
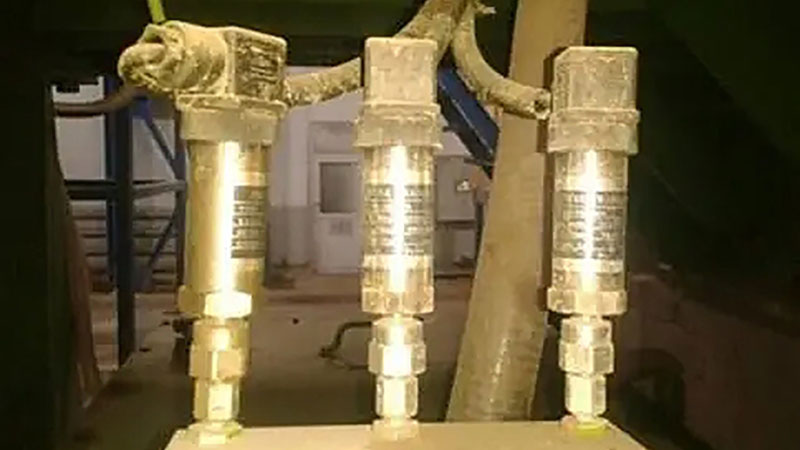
Pressure measurement solutions
Factors to consider when selecting a pressure measurement solution:
- Pressure type: Identify what pressure is being measured, gauge, absolute, or differential.
- Pressure range: The expected pressure range for the application.
- Accuracy requirements: The level of accuracy required for the measurement.
- Process media: The type of fluid or gas being measured (compatibility with the sensor material).
- Temperature range: The operating temperature of the environment.
- Output format: Digital or analog signal required for data acquisition.
Do you need a suitable device to measure vacuum pressure? In industrial production, some equipment needs to work in a vacuum state. At this time, the working equipment or environment needs to be evacuated. In order to accurately control the vacuum degree, vacuum pressure transducers are ideal for detecting the vacuum degree.
Our Sino-Inst offers a wide range of vacuum pressure transducers. Including measuring absolute and compound (negative and positive) pressure ranges. The vacuum range is generally 0~-100Kpa.
If you want to choose the right sensor, choose the product that suits your working conditions. If you have any technical questions, please feel free to contact us!